Filling the needs of Covid-19 vaccine production
With the prospect of not one, but several, COVID-19 vaccines being approved for use in the UK and Ireland imminently, the possibility of bottlenecks in future vaccine production becomes a topic of concern.
The issue of the lead time of key single-use components for the manufacture of COVID-19 vaccines has been addressed by the major suppliers, who have worked tirelessly on prioritisation strategies. And while there are still some areas for improvement, the limitations are well understood by both suppliers and manufacturers of single-use assemblies and components as well as by the vaccine manufacturers themselves.
We even understand the issues of distribution and cold storage of the various vaccine candidates, and the governments and health services in the UK and Ireland have meticulously planned and invested in the delivery and administration of these vaccines to the public.
But what about the final fill and finish of the vaccines themselves? Glass vial manufacturer, Schott, outlined their strategy in June 2020; namely, that they would not deliver stock to candidate manufacturers until it was clear which candidates would be taken forward to commercial production. This strategy would enable Schott to deliver vials where they were needed most and reduce the risk to the supply chain by organisations potentially stock-piling vials that may not be used.
Filling Needles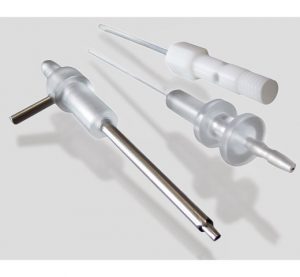
There is another fill/finish bottleneck to consider – filling needles. Re-useable filling needles are still the major option chosen by facilities because they are considered the most cost-effective solution. Single-use alternatives have been available for some time now, however, concerns around extractables and leachables, as well as cost, have prevented many manufacturers from making the switch. Now may be the time to reconsider.
Single-use fill/finish assemblies could help manufacturers meet demand by decreasing downtime between batches and increasing security by decreasing the number of human interventions. Additionally, single-use fill/finish assemblies have been shown to meet the standards of conventional fill/finish processes, ensuring flow-path sterility and integrity, operational safety, and providing the necessary fill-volume accuracy. Benefits include lower operating costs, faster turn-around times, and reduced contamination events, not to mention eliminating the need for plant services and harsh clean-in-place chemicals.
Single-use dosing needles, such as those designed by Overlook Industries Inc. are manufactured in single-use materials as well as in 316L stainless steel. The best-of-both-worlds approach with plastic hub and stainless steel tubing gives OVLK’s Oneshot™ filling needles the freedom of disposability while retaining the utmost level of filling speed, precision and accuracy that advocates of re-useable stainless steel needles expect. The range, available in 24 different sizes, is designed for a variety of filling applications and as a direct replacement for all OEM filling machines, with a wide range of custom tip geometries and coatings for enhanced dispensing.
All Oneshot™ filling needles can be incorporated into customised, sterile, and pre-assembled filling rigs and assemblies, so why not think about making the change to single-use today?
For more information, you can send us an enquiry using our contact form or send us a message via our Chat.